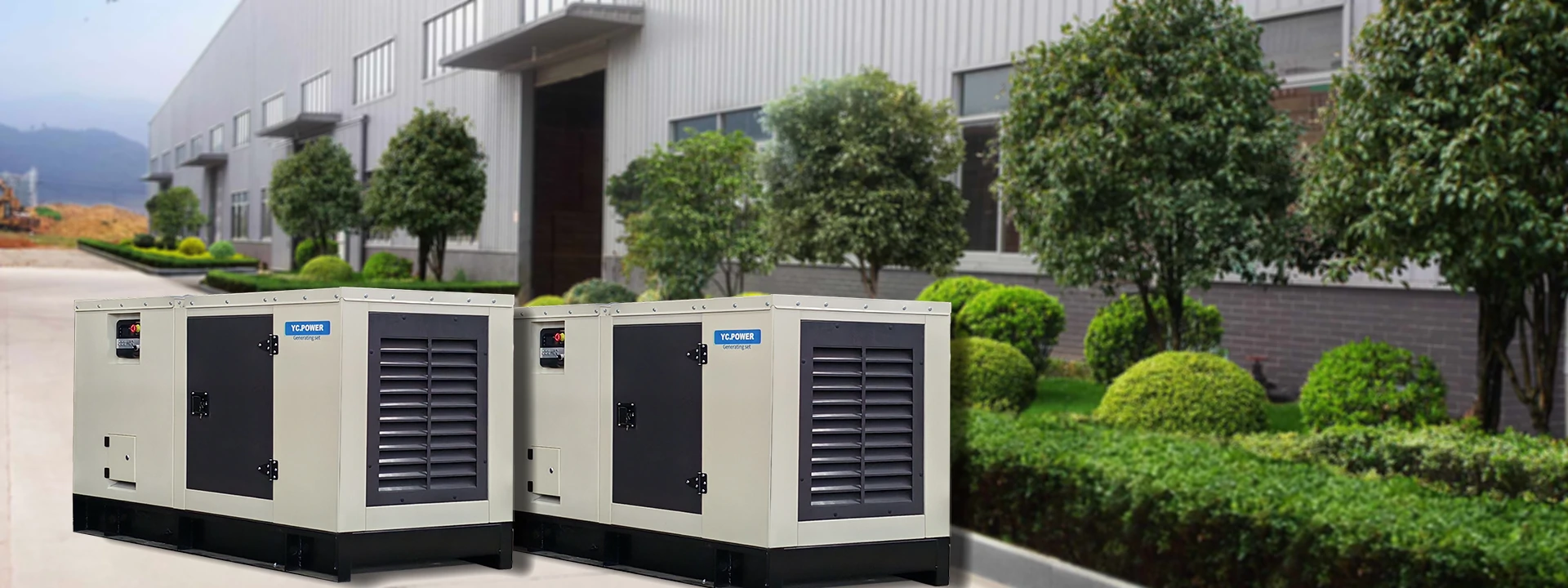
Service Policy
Our service philosophy is “Provide sincere service for the customer, and satisfy customer’s requirements”.
Our company will provide the best service if you choose our products. No matter where your generator set is located, we will provide you with the most timely technical consultation and professional services.
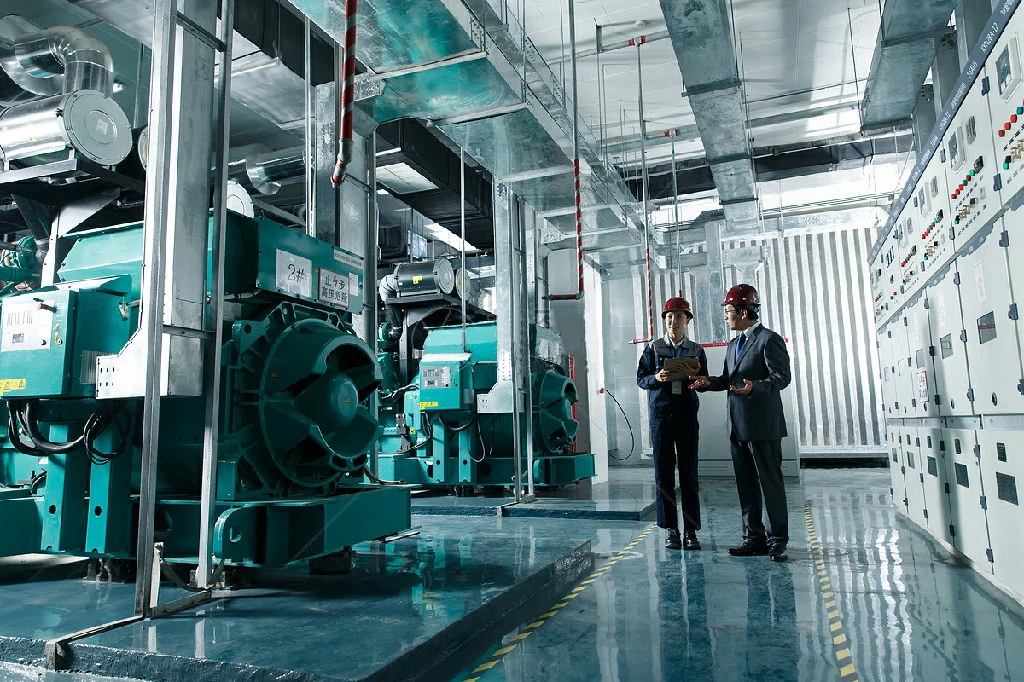
Pre-Sales Service
- Technical Support: We provide pre-sales technical services, including consultation and design assistance, to help customers with conceptual design and equipment selection.
- Equipment Room Design: We assist customers with equipment room layout and arrangement.
- Technical Consultation: We welcome technical inquiries from customers, offering professional guidance as needed.
In-Sales Service
- Production Progress and Quality Assurance: We offer updates on production schedules to ensure product delivery meets quality standards.
- Installation Guidance: After delivery, we provide guidance for product installation.
- Regular Follow-Up: We periodically follow up with customers after delivery to assess equipment performance, evaluate product quality, and offer maintenance suggestions.
After-Sales Service
- Spare Parts: We supply OEM parts, ensuring a reliable source of spare parts for equipment longevity.
- Installation and Commissioning Support: We provide guidance on installation, debugging, and operation of the equipment.
- Training: We guide operation and maintenance training.
- Troubleshooting: We assist with troubleshooting and maintenance as needed.
- Customer Records: We create customer profiles to provide tracking services, conduct regular inspections, and offer lifetime maintenance.
Service Policy
- Warranty Time: one year or 1,000 hours (which comes first)
- If the parts are damaged or other failures of the genset are caused by the manufacturer’s negligence in assembly, improper design and selection of raw materials, the supplier will be responsible for the warranty.
Remarks: Our company will not be responsible for free warranty if the product failure is caused by the following reasons:
- Due to human error
- Failure to perform regular maintenance according to maintenance instructions
- Failures caused by self-disassembly, repair, and installation
- Failure caused by failure to replace wearing parts of diesel generator sets in time
- Failures caused by abnormal reasons (including poor power environment, moving, collision, etc.)
- Force majeure: all failures caused by natural disasters such as earthquakes, fires or force majeure such as accidents.
Spare Parts
- Original manufacturer authorized spare parts supply service
- Rapid response in 24 hours global consignment
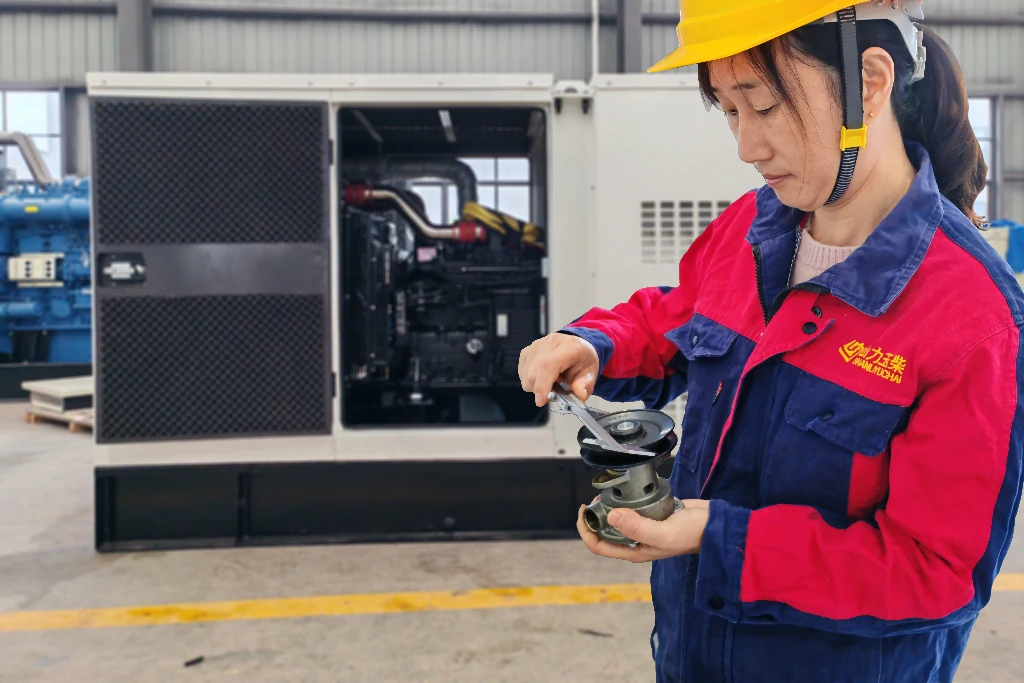
Maintenance
Routine Maintenance
- Check for loose bolts on rotating parts and tighten them as needed.
- Check the oil pan level, and add oil if low.
- Inspect fuel tank and water tank levels.
- Check oil and water pipe joints and intake/exhaust seals; remove surface oil stains and dust.
Professional Maintenance (every six months or annually)
- Inspect water tank, battery, oil, and air levels.
- Conduct a 5-10 minute no-load run to ensure sufficient lubrication, assessing the unit’s condition by sound, visual inspection, and smell.
- Replace air filter, diesel filter, oil filter, water filter, and other consumables.
- Replace radiator coolant or protective solution.
- Refill battery fluid or distilled water to ensure optimal condition.
Level-A Maintenance (50-80 hours after operation)
- Clean or replace the air filter if needed.
- Replace diesel filter, air filter, and water filter.
- Check drive belt tension and adjust if necessary.
- Add lubricant and replace coolant.
Level-B Maintenance (250-300 hours after operation)
- Remove carbon deposits from the combustion chamber and ventilation flue.
- Clean piston, cylinder, and other key parts, checking for wear.
- Check for any looseness at the main bearing of the rolling element.
- Clean any scale or sediment from the coolant conduit.
Level-C maintenance (500-1000 hours)base on Level-A & B
- Check and adjust the injector angle;
- Wash the fuel tank;
- Wash the oil pan;
- Check the atomizing condition of sprayer.
Maintenance Notes
- The service personnel should carefully read the Genset Operation and Maintenance Manual provided by manufacturer and arrange the maintenance service according to the requirements of manual;
- Insulated resistance between the winding and earth should be measured if genset hasn’t worked for long time or being in wet condition. The insulation value should not less than 1.5MΩ. Disconnect the negative terminal of battery before the measurement;
- Aperiodically clean the dust and oily dirty ;
- The generator must not be affected with damp.Metal fragments, moisture and other harmful gas should be prevent form getting into genset .When generator is working , ensures that it is at good ventilation. Any covering is not allowed on the genset surface in case of the cooling and ventilation being affected;
- The generator battery should be kept away from heat sources, and ventilation should be maintained during charging and use.